经典案例
圆形的工作台边,几个人组成的工作单元完成全部的组装工作。没有了流水线,没有了无人帮运机,也不见了自动化仓库,单元式生产开始成为佳能新的选择。
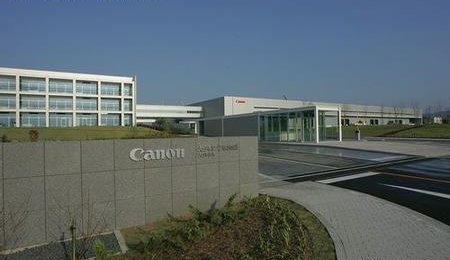
社长俯身求教
“一提起降低成本,似乎马上就想到产业外输化,但是这样做不过是利用了外输地优越的生产条件,公司本身的生产力并没有改进。”每次回国,看到本国公司空洞化,工厂一片惨淡的情形,痛心而由衷地期望进行一次能够真正提高佳能生产效率的革新。
他仔细地分析了当前的困境:面对产品更新换代加快,品种日趋多样化的势头,以少品种、大产量为前提的流水线生产方式开始显得捉襟见肘,它不仅仅会导致销售机会丧失,还有可能陷入大量库存的危机。如果一味依赖巨额投资的大型生产设备,投资调配就会出现困难。
所以,寻找一种灵敏的、富有弹性的、能够满足小产量、多品种要求的生产方式,成了佳能最迫切的希望。
此时,一家电子零部件厂的代表团来佳能参观,他们对佳能的自动化流水线给予了毫不留情的批评:“这些长长的传送带根本就没必要,佳能完全是在浪费钱”,“把‘无人帮运’这种无聊的东西都合理化了,再也找不到这样愚蠢的事了。”
面对如此辛辣的批评,社长决定和各位董事一起看看那家电子零部件工厂和一家大型电机制造工厂。他们惊奇地发现对方已经停止了传送带流水作业方式,采取了一种新的、被称为“单元生产”的生产方式--由几个人组成的生产小组从事全部复杂工程,生产出完整产品。
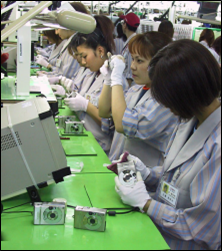

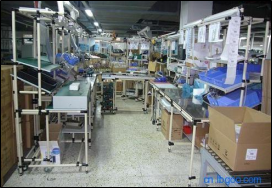
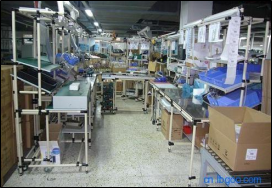
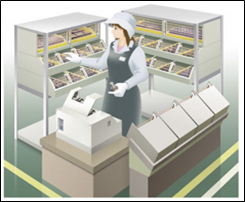
比如日本市场曾经流行的超薄翻盖手机P504i的组装就采用了单元式生产方式。3名女工站在不到3米长的工作台前组成一个单元,所有的手机装配流程都由她们完成。第一名女工的工作是把一块电路板装进上盖板,装好摄像头,拧紧螺丝,完成后放到第二名女工的手边;第二名女工用联线把上下盖板连接起来,传给第三名女工,同时顺手帮她拿上一块电路板;第三名女工把电路板装进下盖板,拧好螺丝,手机装配完成。整个过程不到半分钟,这样一个单元一天可装配手机900部,而以前一条流水线需要14个人作业,每天只能生产1300部。所需零部件都堆放在工作台上,工人不用移动位置,这就减少了机器、半成品和人员移动的损耗。而且还大大节约了空间,装配车间的1/3因此空闲下来。
在参观完工厂后,社长决定从长浜佳能开始进行生产革新。1998年初,革新运动正式开始。
表面看来,单元式生产方式对流水线生产方式的否定是生产流程技术性的变化。实质上,这是一种制度创新,是生产观念的革新。单元式生产方式并不像流水线生产方式那样,需要高度的机械化和自动化的流水线,而且很多人也知道这样一种方法,但是为什么大多数人都不愿意去实践呢?因为过去流水线生产方式取得了辉煌的成功。大多数企业被“福特主义”神话所束缚,像佳能这种不断扩大、发展的公司,大型的流水线生产还是一种发展、进步和实力的象征。
然而这一思维却忽略了当今时代个性化需求所带来的巨大变化。佳能从现金流通经营方面考虑,把那些固定大量资金的重、厚、长、大的设备、库存品、半成品视为“恶”,对于样品变更反应迟钝的生产方式也视为“恶”,由于生产过剩将多余的库存品强塞给销售公司来提高销售额的做法更是“恶的极至”。所以,当他发现单元式生产方式后,就毫不犹豫地对传统的流水线生产方式进行了质疑,分析认为:虽然像汽车这样大型产品的组装,单元式生产方式显得有些力不从心,但对于复印机这类产品而言,单元式生产方式加以改进是非常合适的。
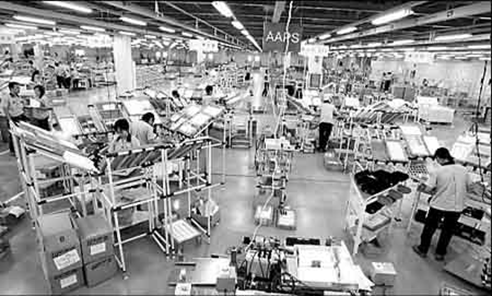
流水线撤除行动
“如果生产革新一开始就在整个公司展开,可能会引起强烈的反对,反而会有失败的危险。”考虑到这一点,社长决定从首先提出改革方案的周边机器事业总部开始改革。
但了解到当时生产总部正在进行“新佳能生产系统的革新运动”,并且取得了一定成果。如果现在马上叫他们进行单元式生产变革,恐怕很难有回应。于是,他干脆避开了总公司的工厂,而把子公司长浜佳能作为了改革的“先头部队”,采用先从周边工厂点燃火种,再扩展到整体的战略。
长浜佳能的生产部长考虑到革新的困难,决定采取逐步推进的方式,从“节省空间”运动切入。
于是他们除去流水线上多余的动作以及生产现场利用无人运送机搬运零件等无用环节。一方面减少了流水线作业者之间的距离,另一方面重新安排工厂的陈设,缩短零件移送的距离,这样一来作业者就不会过于枯燥,工作效率也提高了。由于工厂节约出很多的空间,原本安置在别处的捆包生产线也搬到了激光打印机主机组装生产线的旁边,两者结合使得作业效率一下子提升了。
与此同时,生产主要零件的流水线组装方式向单元式转换的试验也正式开始。为了降低风险,长浜佳能决定从相对简单的激光扫描仪组装生产线开始。因为激光扫描仪组装生产线只有20米,是扫描仪生产线的1/10。
单元式生产进一步缩短了激光扫描仪生产线的距离,以前20米长的流水生产线,现在只用10米长就可以,实际上,相同生产线的产量就是过去的2倍;另外,两边堆放的物料也缩短一半,节省了产品停留在传送带上的时间,节省了整体成本,提高了效率。而且,工厂管理人员、监督人员和技术人员以3个月为一个周期对有浪费的环节进行改善。
当初步的试验顺利进行的时候,打印机主机组装生产线的试验也同步开始。他们不是一口气急于将6条生产线一次性地转为单元式,而是一条一条依次进行变更,也不是极端地采用一个人为一个单元的方式,而是改成10个人一个小组进行作业。
试验开始得并不顺利,从各种数据看,生产效率不仅没有明显提高,反而有所降低。但是“救命女神”最终出现了。生产现场的女工组成了一个10人女性生产小组,她们在每次作业结束后,自主地召开一个小型讨论会,摸索改善的方法。与此同时,现场生产的工人们尽管有所不满,但也渐渐地熟悉了这种作业方式,生产现场开始出现工人积极工作的氛围。在连续召开三天讨论会后,女性生产小组终于提前完成了生产任务,受到她们的激励,其他现场的工人也开始积极地投入工作。
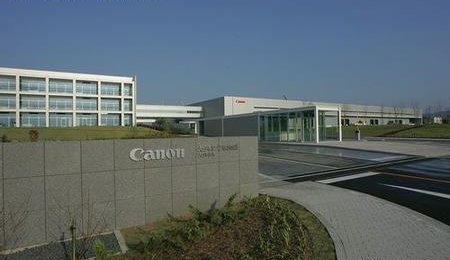
社长俯身求教
“一提起降低成本,似乎马上就想到产业外输化,但是这样做不过是利用了外输地优越的生产条件,公司本身的生产力并没有改进。”每次回国,看到本国公司空洞化,工厂一片惨淡的情形,痛心而由衷地期望进行一次能够真正提高佳能生产效率的革新。
他仔细地分析了当前的困境:面对产品更新换代加快,品种日趋多样化的势头,以少品种、大产量为前提的流水线生产方式开始显得捉襟见肘,它不仅仅会导致销售机会丧失,还有可能陷入大量库存的危机。如果一味依赖巨额投资的大型生产设备,投资调配就会出现困难。
所以,寻找一种灵敏的、富有弹性的、能够满足小产量、多品种要求的生产方式,成了佳能最迫切的希望。
此时,一家电子零部件厂的代表团来佳能参观,他们对佳能的自动化流水线给予了毫不留情的批评:“这些长长的传送带根本就没必要,佳能完全是在浪费钱”,“把‘无人帮运’这种无聊的东西都合理化了,再也找不到这样愚蠢的事了。”
面对如此辛辣的批评,社长决定和各位董事一起看看那家电子零部件工厂和一家大型电机制造工厂。他们惊奇地发现对方已经停止了传送带流水作业方式,采取了一种新的、被称为“单元生产”的生产方式--由几个人组成的生产小组从事全部复杂工程,生产出完整产品。
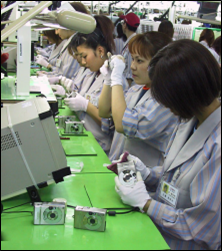

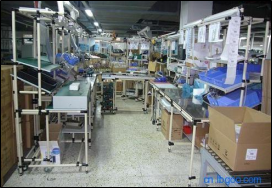
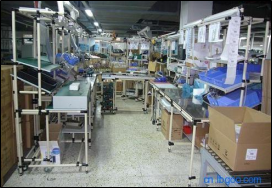
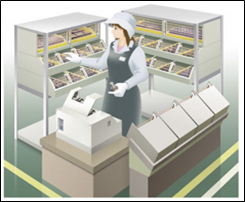
比如日本市场曾经流行的超薄翻盖手机P504i的组装就采用了单元式生产方式。3名女工站在不到3米长的工作台前组成一个单元,所有的手机装配流程都由她们完成。第一名女工的工作是把一块电路板装进上盖板,装好摄像头,拧紧螺丝,完成后放到第二名女工的手边;第二名女工用联线把上下盖板连接起来,传给第三名女工,同时顺手帮她拿上一块电路板;第三名女工把电路板装进下盖板,拧好螺丝,手机装配完成。整个过程不到半分钟,这样一个单元一天可装配手机900部,而以前一条流水线需要14个人作业,每天只能生产1300部。所需零部件都堆放在工作台上,工人不用移动位置,这就减少了机器、半成品和人员移动的损耗。而且还大大节约了空间,装配车间的1/3因此空闲下来。
在参观完工厂后,社长决定从长浜佳能开始进行生产革新。1998年初,革新运动正式开始。
表面看来,单元式生产方式对流水线生产方式的否定是生产流程技术性的变化。实质上,这是一种制度创新,是生产观念的革新。单元式生产方式并不像流水线生产方式那样,需要高度的机械化和自动化的流水线,而且很多人也知道这样一种方法,但是为什么大多数人都不愿意去实践呢?因为过去流水线生产方式取得了辉煌的成功。大多数企业被“福特主义”神话所束缚,像佳能这种不断扩大、发展的公司,大型的流水线生产还是一种发展、进步和实力的象征。
然而这一思维却忽略了当今时代个性化需求所带来的巨大变化。佳能从现金流通经营方面考虑,把那些固定大量资金的重、厚、长、大的设备、库存品、半成品视为“恶”,对于样品变更反应迟钝的生产方式也视为“恶”,由于生产过剩将多余的库存品强塞给销售公司来提高销售额的做法更是“恶的极至”。所以,当他发现单元式生产方式后,就毫不犹豫地对传统的流水线生产方式进行了质疑,分析认为:虽然像汽车这样大型产品的组装,单元式生产方式显得有些力不从心,但对于复印机这类产品而言,单元式生产方式加以改进是非常合适的。
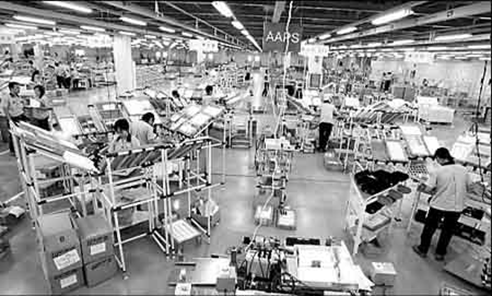
流水线撤除行动
“如果生产革新一开始就在整个公司展开,可能会引起强烈的反对,反而会有失败的危险。”考虑到这一点,社长决定从首先提出改革方案的周边机器事业总部开始改革。
但了解到当时生产总部正在进行“新佳能生产系统的革新运动”,并且取得了一定成果。如果现在马上叫他们进行单元式生产变革,恐怕很难有回应。于是,他干脆避开了总公司的工厂,而把子公司长浜佳能作为了改革的“先头部队”,采用先从周边工厂点燃火种,再扩展到整体的战略。
长浜佳能的生产部长考虑到革新的困难,决定采取逐步推进的方式,从“节省空间”运动切入。
于是他们除去流水线上多余的动作以及生产现场利用无人运送机搬运零件等无用环节。一方面减少了流水线作业者之间的距离,另一方面重新安排工厂的陈设,缩短零件移送的距离,这样一来作业者就不会过于枯燥,工作效率也提高了。由于工厂节约出很多的空间,原本安置在别处的捆包生产线也搬到了激光打印机主机组装生产线的旁边,两者结合使得作业效率一下子提升了。
与此同时,生产主要零件的流水线组装方式向单元式转换的试验也正式开始。为了降低风险,长浜佳能决定从相对简单的激光扫描仪组装生产线开始。因为激光扫描仪组装生产线只有20米,是扫描仪生产线的1/10。
单元式生产进一步缩短了激光扫描仪生产线的距离,以前20米长的流水生产线,现在只用10米长就可以,实际上,相同生产线的产量就是过去的2倍;另外,两边堆放的物料也缩短一半,节省了产品停留在传送带上的时间,节省了整体成本,提高了效率。而且,工厂管理人员、监督人员和技术人员以3个月为一个周期对有浪费的环节进行改善。
当初步的试验顺利进行的时候,打印机主机组装生产线的试验也同步开始。他们不是一口气急于将6条生产线一次性地转为单元式,而是一条一条依次进行变更,也不是极端地采用一个人为一个单元的方式,而是改成10个人一个小组进行作业。
试验开始得并不顺利,从各种数据看,生产效率不仅没有明显提高,反而有所降低。但是“救命女神”最终出现了。生产现场的女工组成了一个10人女性生产小组,她们在每次作业结束后,自主地召开一个小型讨论会,摸索改善的方法。与此同时,现场生产的工人们尽管有所不满,但也渐渐地熟悉了这种作业方式,生产现场开始出现工人积极工作的氛围。在连续召开三天讨论会后,女性生产小组终于提前完成了生产任务,受到她们的激励,其他现场的工人也开始积极地投入工作。
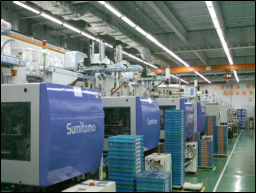
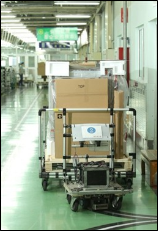